Slicer in Grasshopper for Laser Cutting
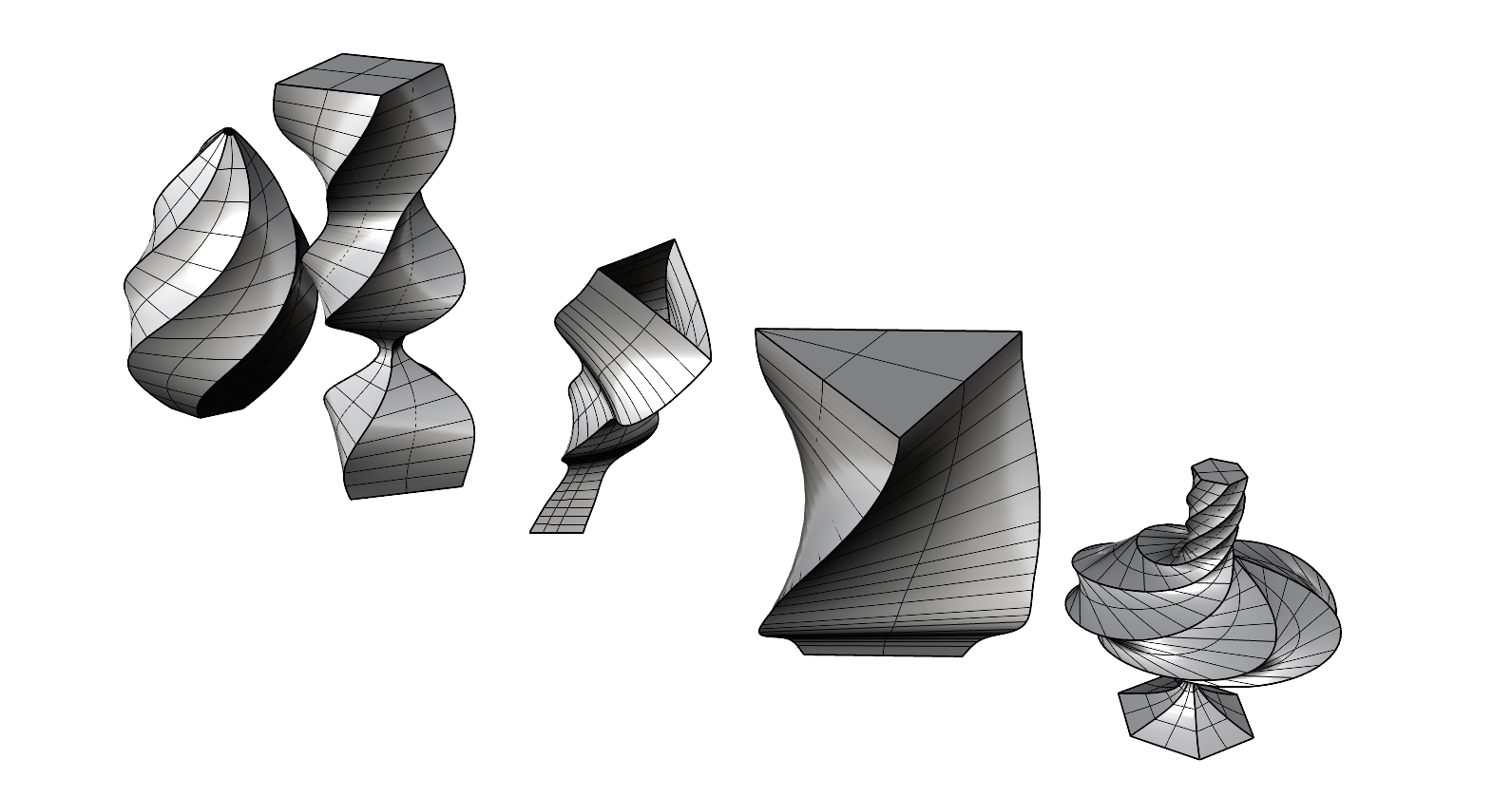
Task 1 - Parametric Object
The first step was to generate some parametric objects. I started with a simple line between two point constructs between which are several points based on a line dividing component. At each point along the line, a polygon is drawn according to a randomized polygon builder node. The following polygonal extrusion (lofted and capped) is twisted using a cool knob to control the angle. In total, there are 12 parameters that can be modified to change the resulting object, the most influential of which is the seed input to the random function.
Object 1:
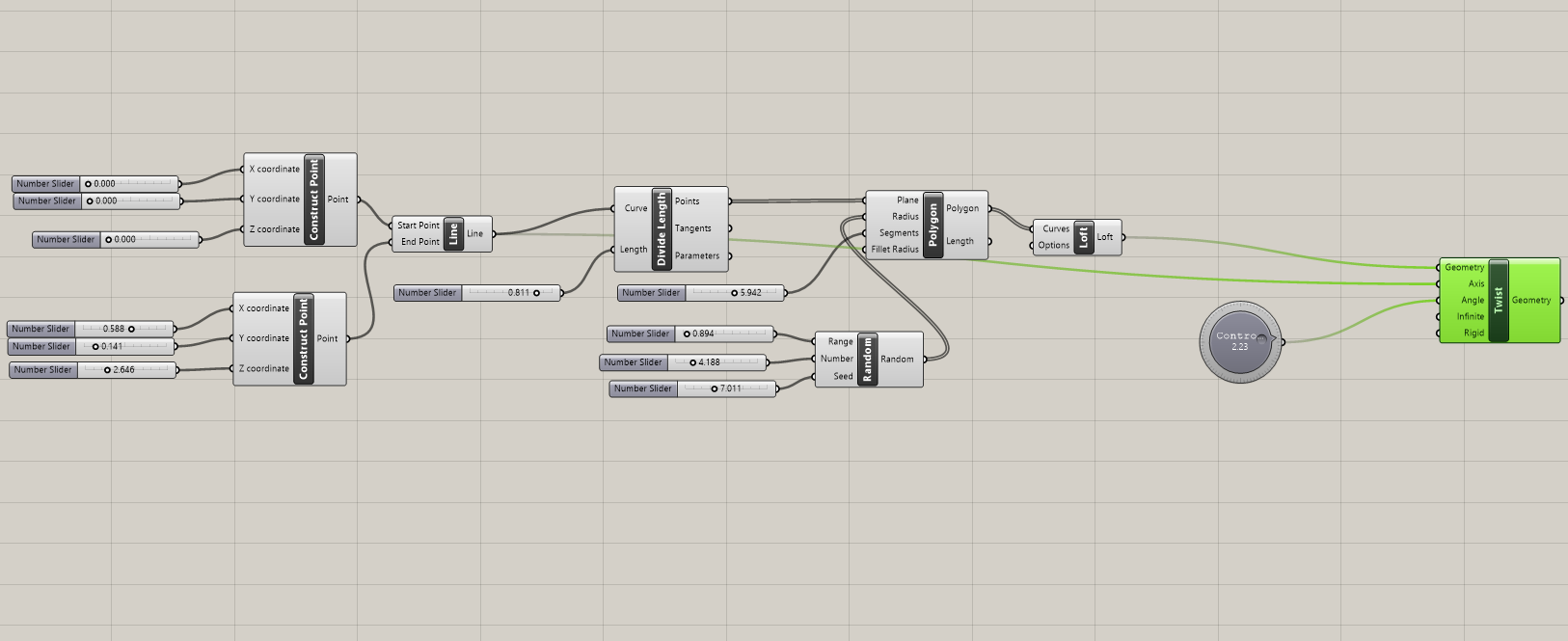
Output:
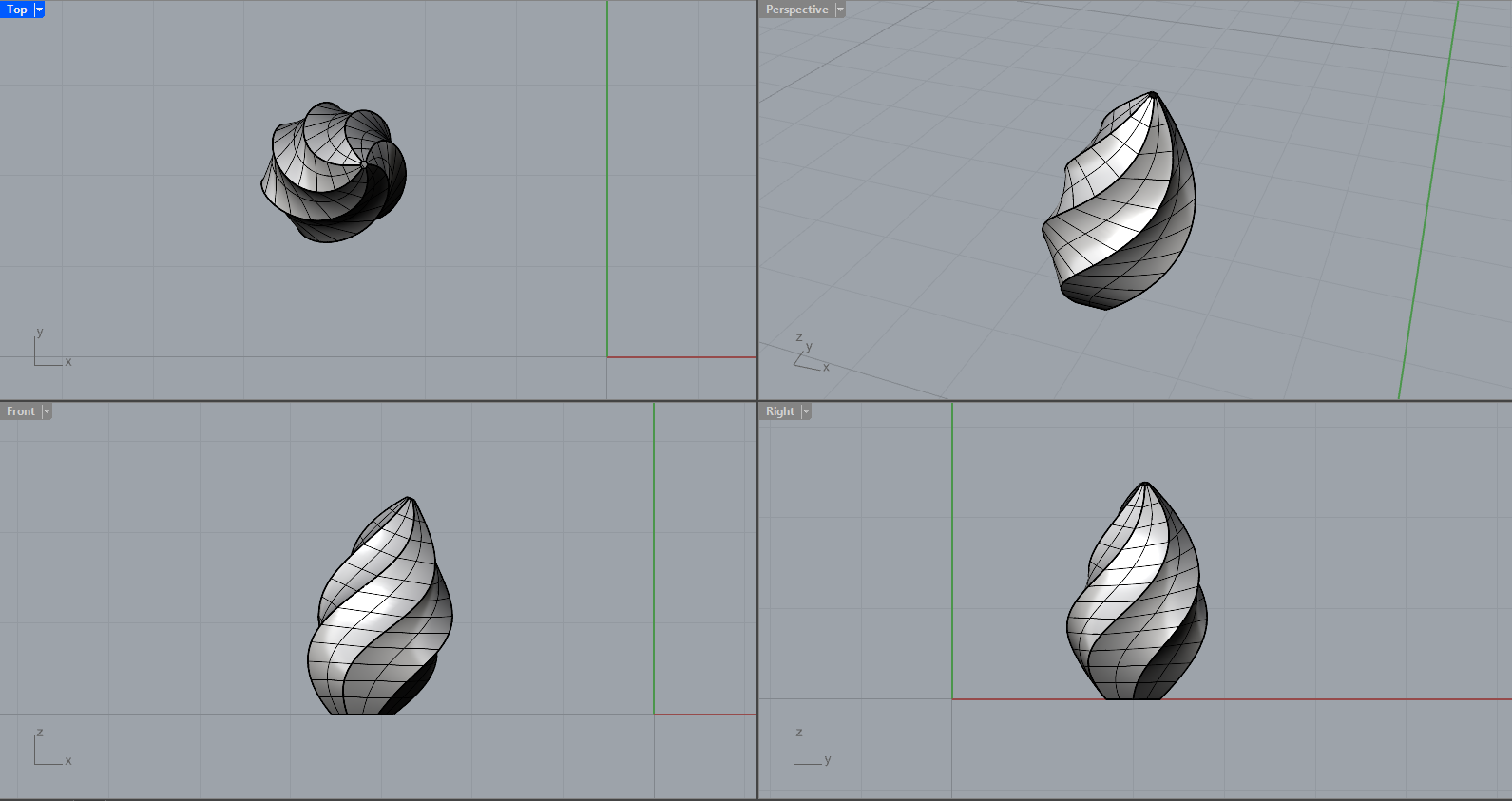
Object 2:
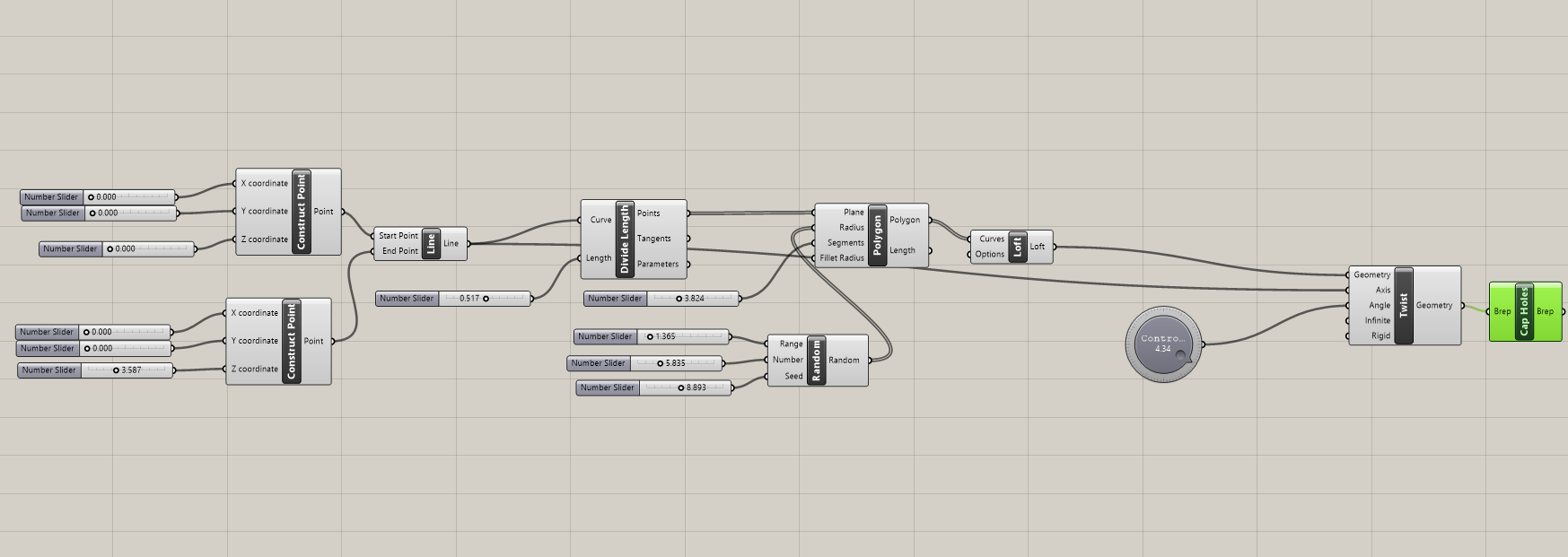
Output:
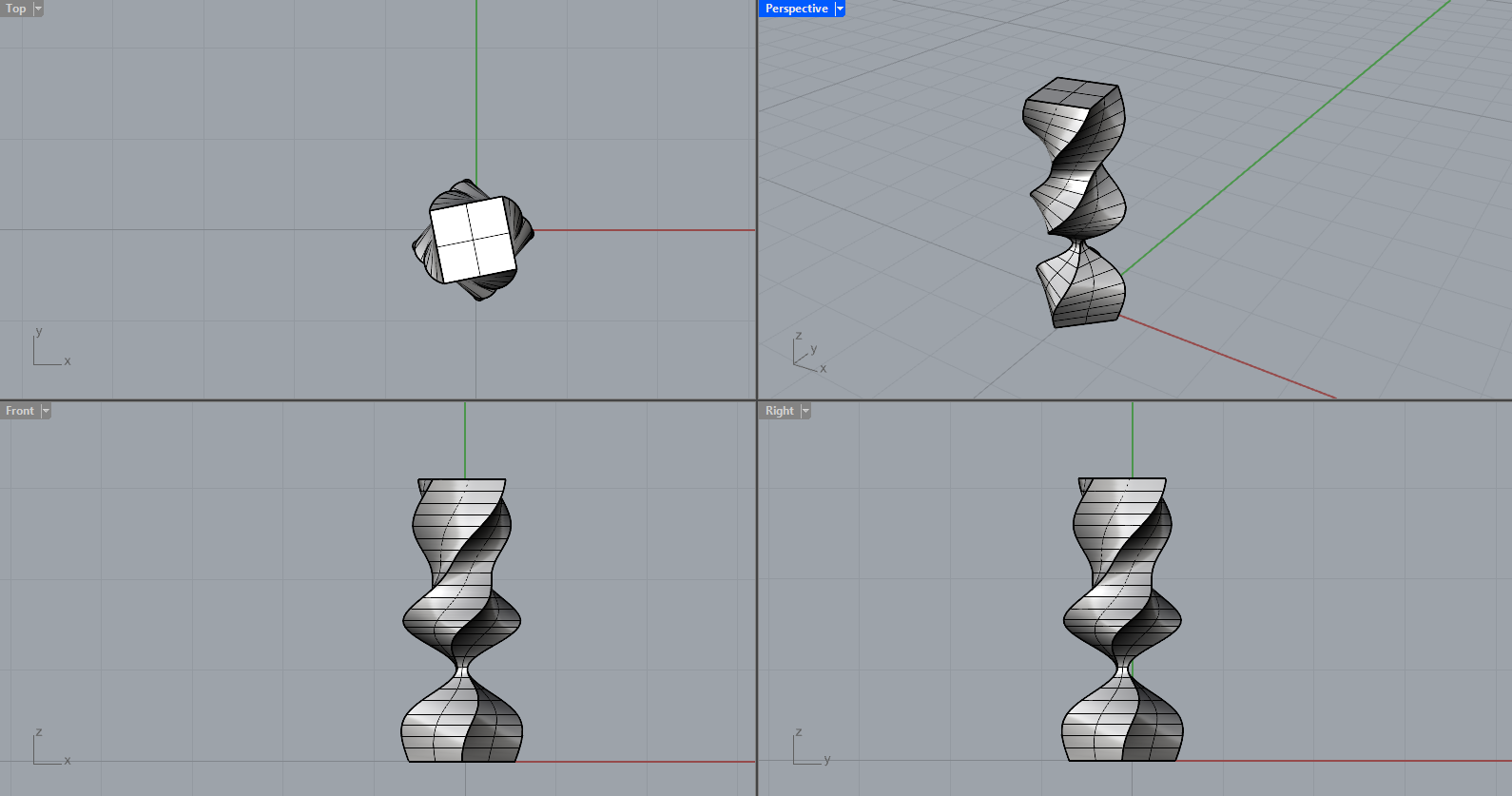
Object 3:
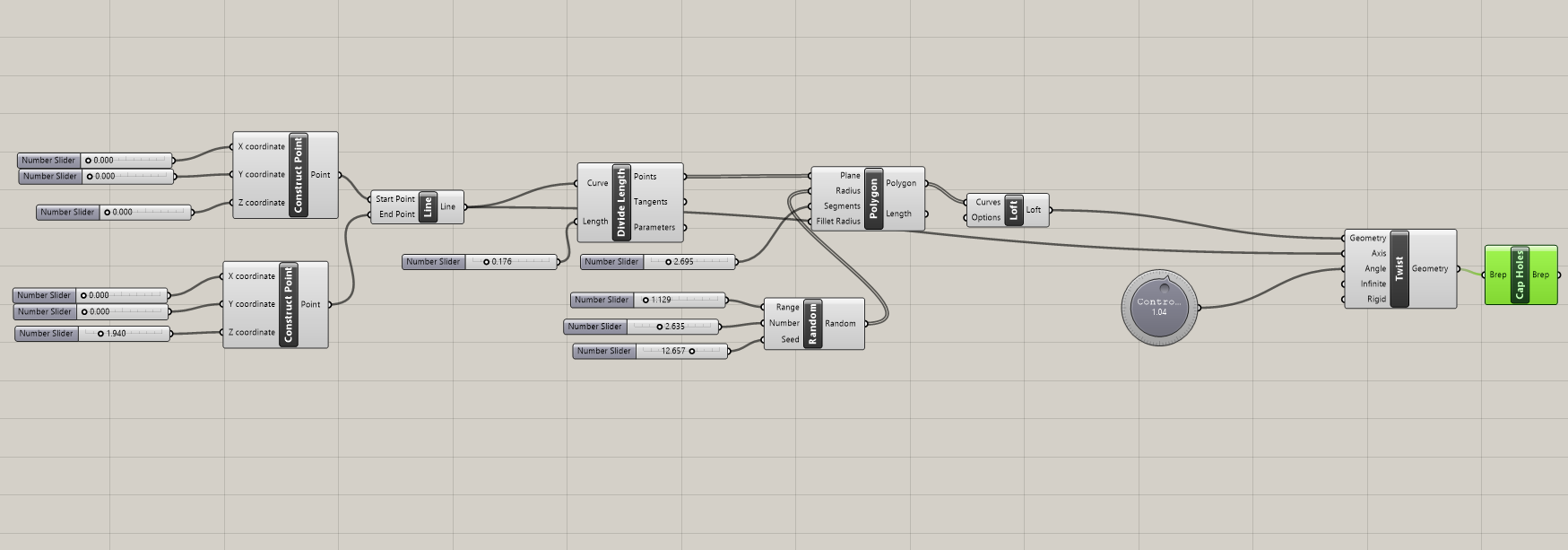
Output:
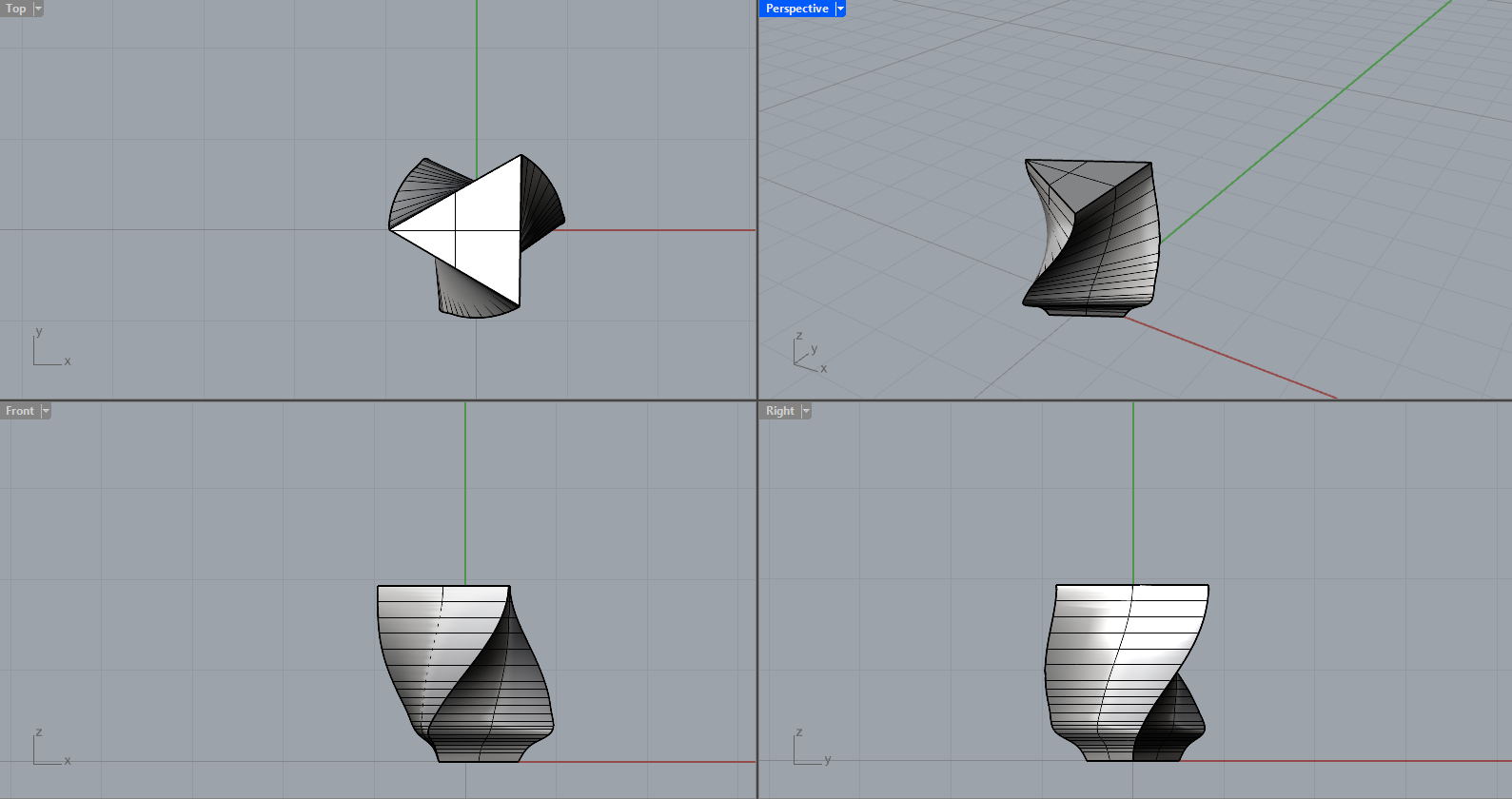
Object 4:
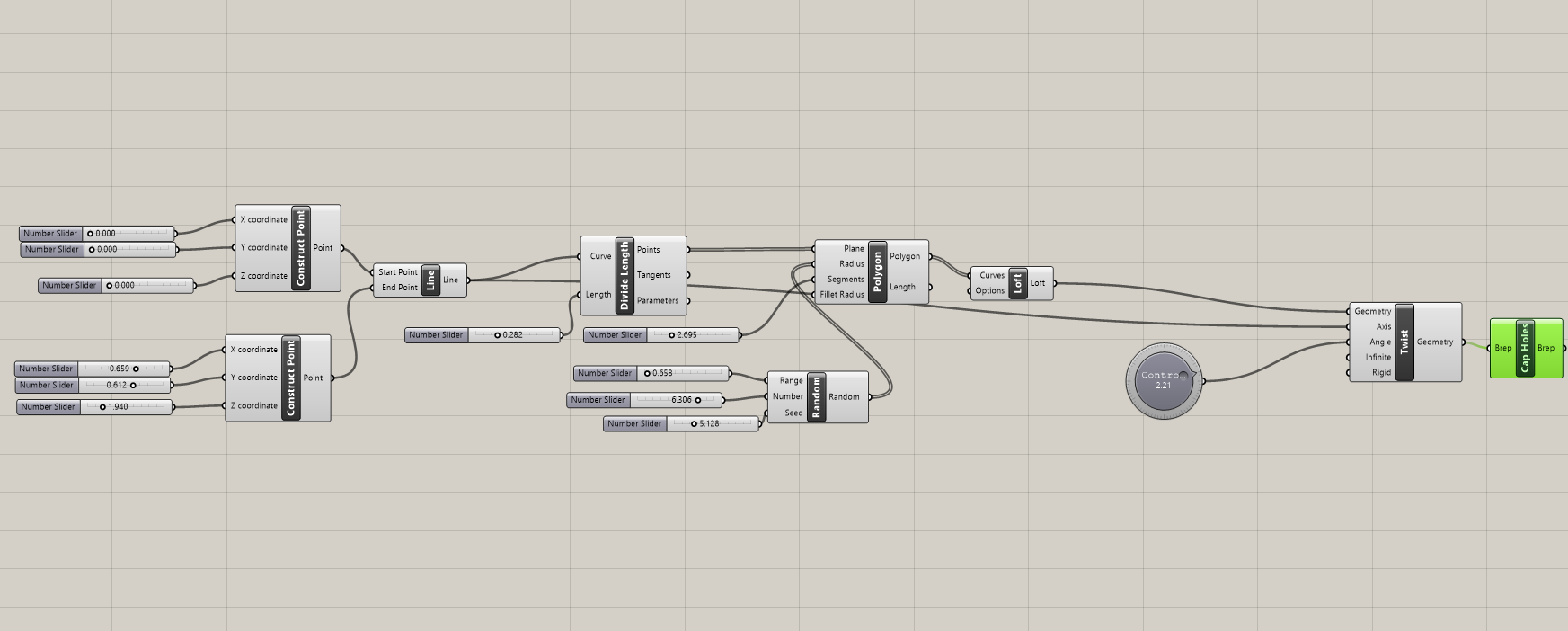
Output:
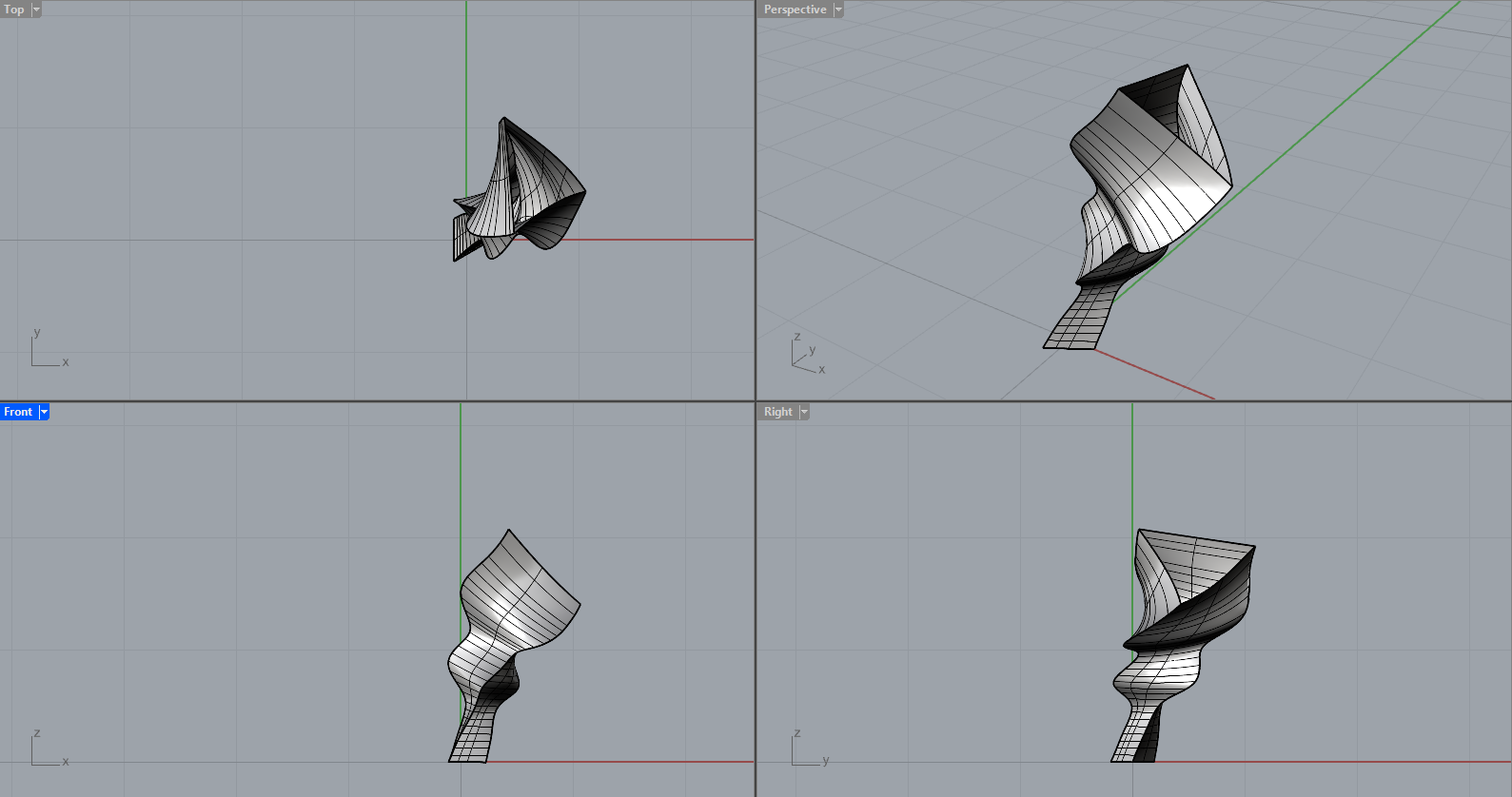
Object 5:
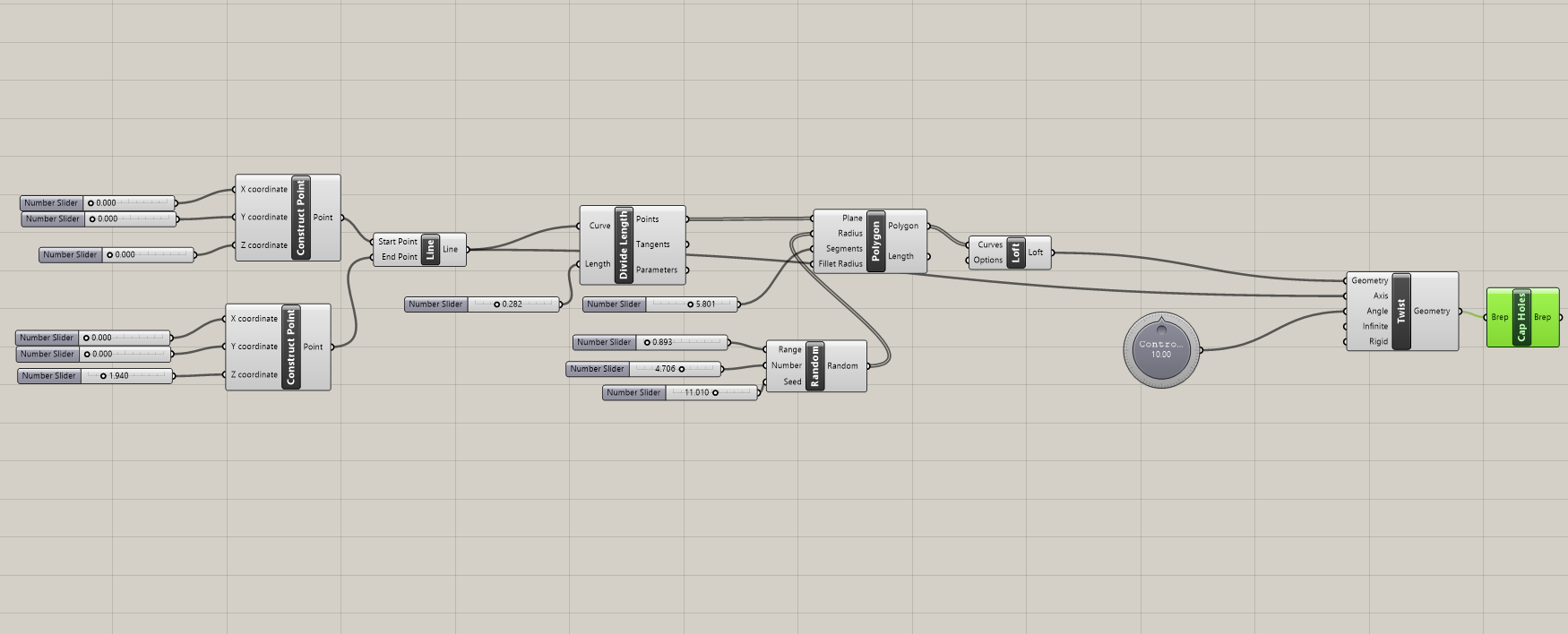
Output:
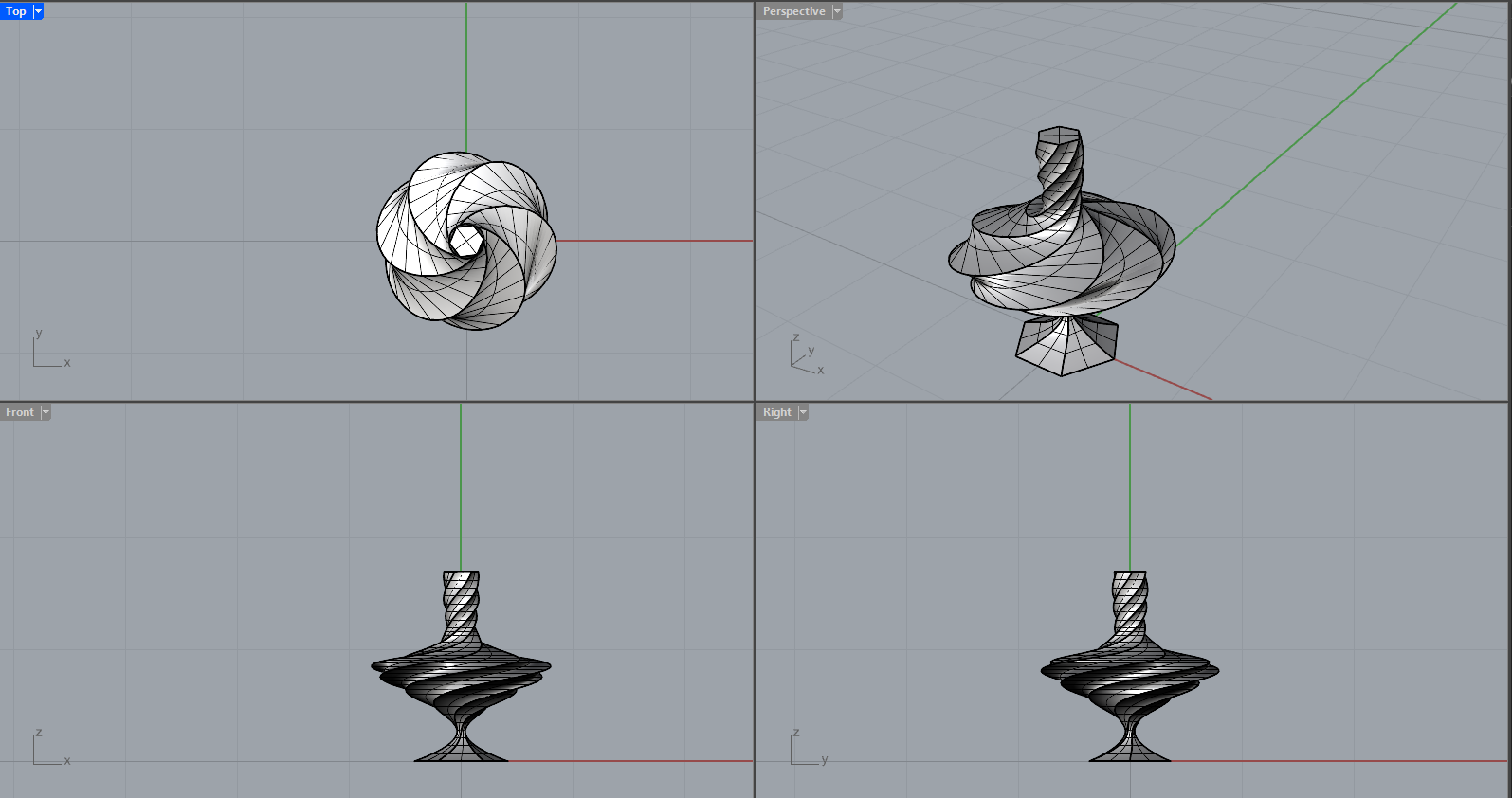
Task 2 - Slicing
The next step was to take the resulting geometry and slice it at regular intervals dependent on the material thickness of the laser cutting material (I used 3 mm for standard acrylic sheeting). This is done by using the same axis as the original object, but running a new line division through it. Using planes and BREP intersections, the first glimmer of hope appears through the transulent red of the preview. The final step is to organize these cross-sectional polygons on the XY plane, and use Mass Addition Partial Output to move the polygons accorss the XY plane so they don't overlap, and thus can be exported. They are also numbered.
Code and Output Images:
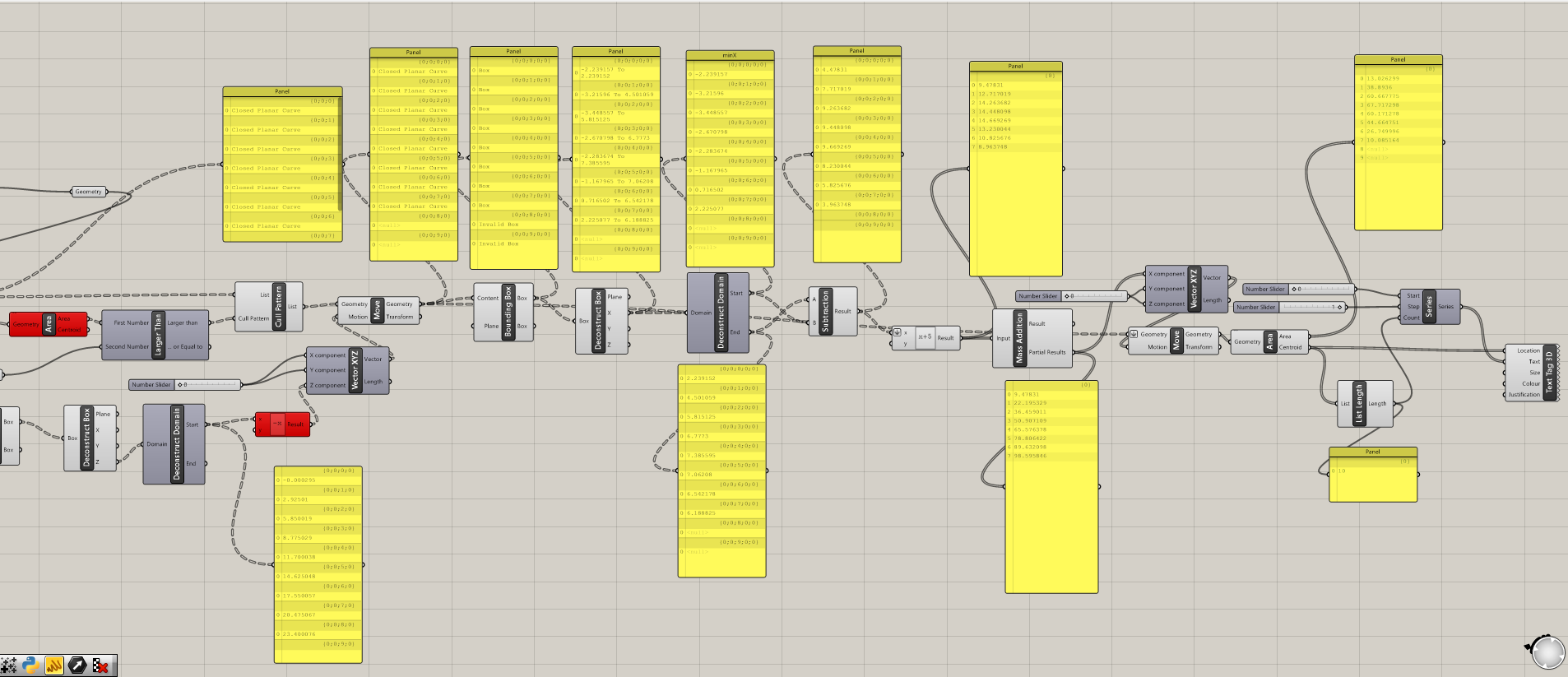
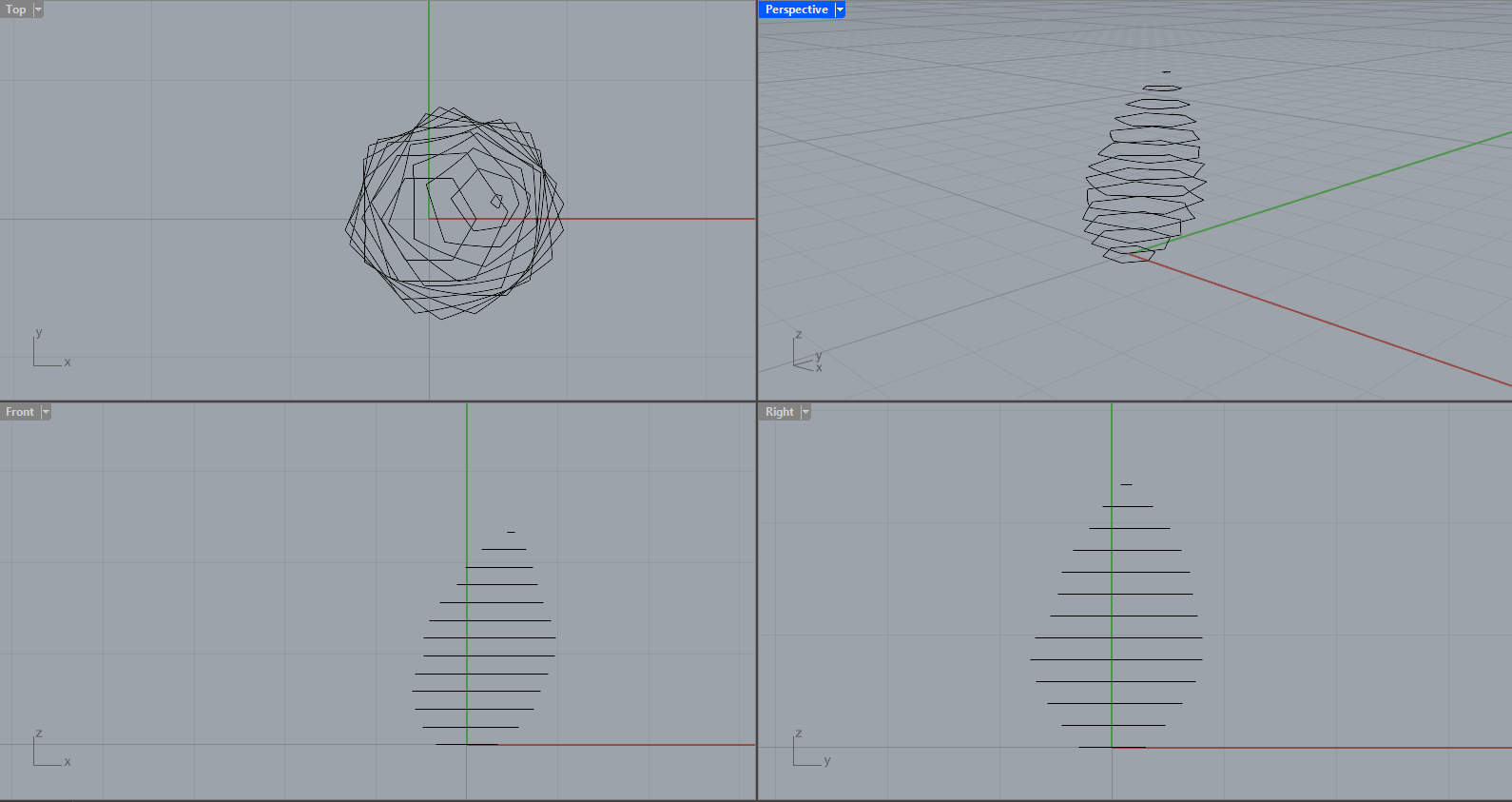
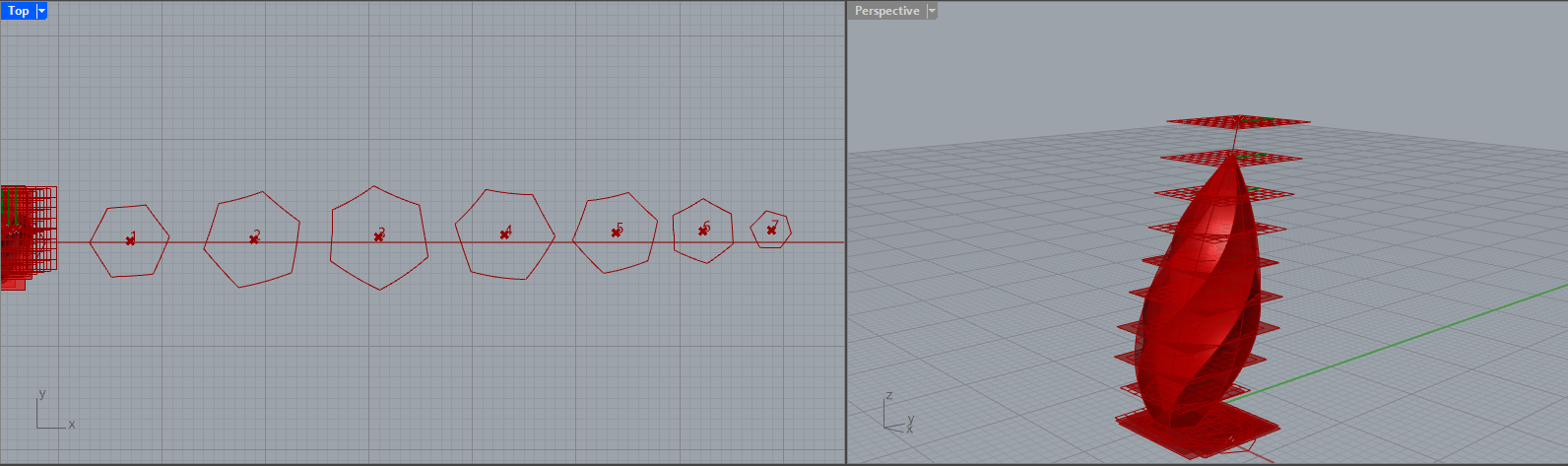

Conclusion
[]